1. Real view:
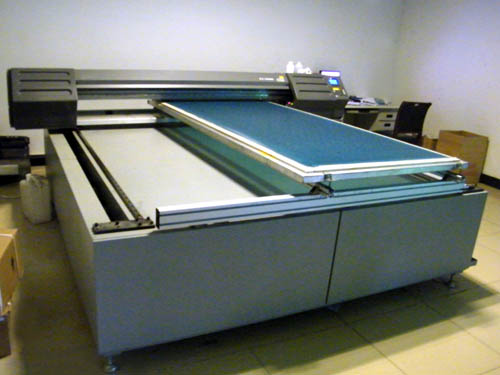
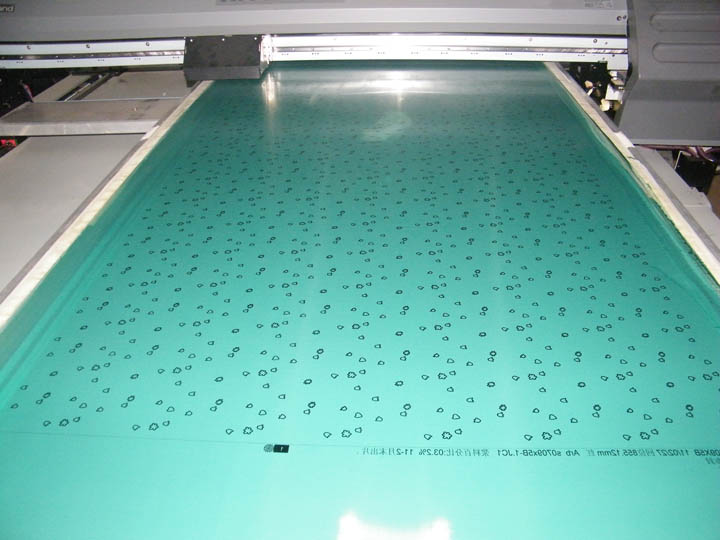
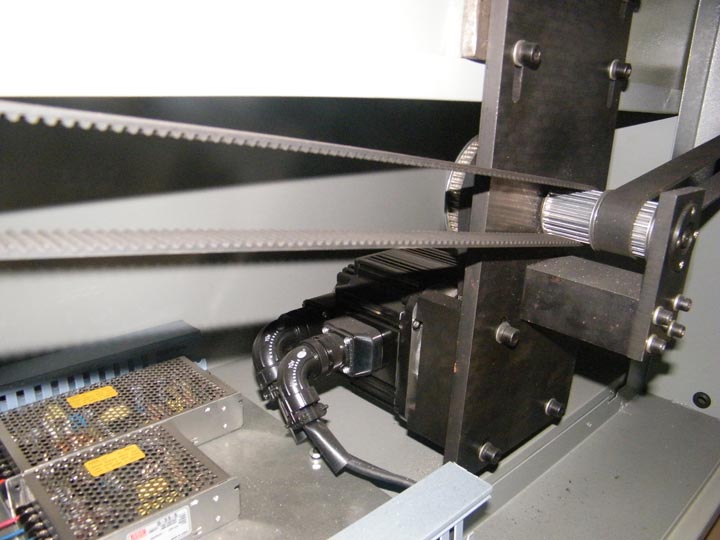
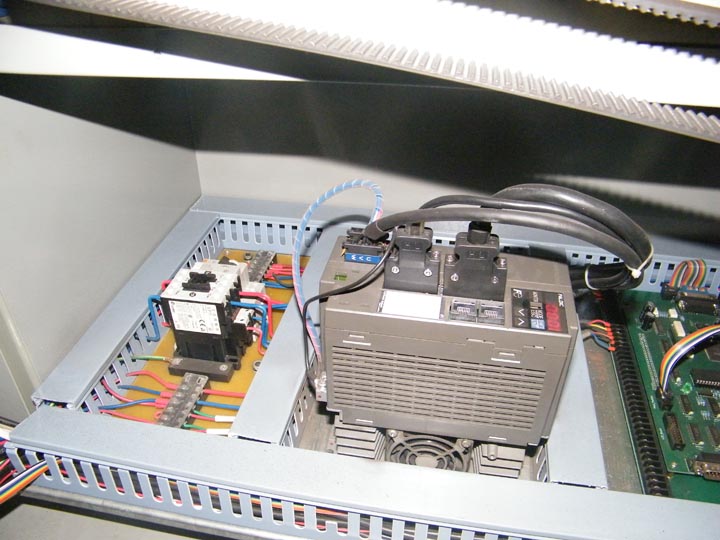
2. What is Focus CTS computer to screen iamging direct to screen imaging flat bed inkjet engraver?
CTS is the short for Computer-to-Screen, also called as filmless computer to screen imaging system, direct to screen imaging system, flatbed inkjet engraver, digtal inkjet screen plate making system, filmless screen imaging system... Following in the footsteps of offset lithography, the screen printing industry has seen a dramatic technology shift in its pre-press department with the advancement and acceptability of CtS devices. One of the biggest advantages in using a CtS system is the use, storage and potential for film loss or damage is eliminated, reducing the overall cost of making a screen.
CtS systems are also accurate and repeatable. Because the artwork is imaged directly to the coated screen, a vacuum blanket is not required during exposure, which removes any possibility of film distortion. Since there is no film, exposure time decreases and the amounts of light scatter and stencil undercutting are greatly reduced. Film dust and scratches also aren't a headache for the screen maker.
The four primary imaging technologies used in CtS systems are inkjet, thermal, Digital Light Processing (DLP) and laser. Each has its advantages and disadvantages, but there is not doubt our industry is moving heavily toward CtS in general. What appears to be cutting-edge today will be commonplace tomorrow, as more companies adopt these technological advantages to increase their margins and reduce costs.
Inkjet employs the use of conventional, water-based ink or solid wax, which is jetted directly to a coated screen and exposed. Devices using conventional ink typically utilize Epson print heads, and can reach resolutions of 600dpi to 1440dpi. They are a cost-effective alternative to solid wax systems, which have slightly higher consumable costs. Since the ink is water-based, environmental conditions play a crucial role as day-to-day fluctuations in humidity can make repeatability a bit more challenging. On the upside, print head replacement in water-based systems is relatively inexpensive when compared with wax. Those prices range from a few hundred dollars. it is also cost less compare with the traditoncal silk screen printing film expose way, as film cost, expose machine cost, expose time cost, labour cost.
Solid wax systems have a maximum resolution of 1300 dpi and employ the use of water-soluble wax tablets, which are heated in the CtS device. The molten wax is jetted onto a coated screen where it solidifies, producing great detail at densities at or above 4.5 D-max. Imaging speed will vary based on the selected resolution and number of nozzles in the print head, but printing speeds of 1-square-meter (10.75-square-feet) in a few minutes are not uncommon.
consider how much your company spends on film each year; an inkjet system may pay for itself in a very short time. Several hundred early adopters of these systems have converted from traditional film - with costs of about $10 per square meter ($1 per square foot) - to inkjet, and are now spending as little as 5 cents per screen in consumables.
3. The advantage of FOCUS CTS-180ES digital filmless computer to screen, direct to screen imaging system
1. Low cost. It is save a big cost for the film, the film is made from silver metal. price almost from 6$ to 10$ per square meter according to different quality, it will cost 1$ per squre foot. but use the flat bed inkjet engraver only cost 5cents per square meter, it is use the digital water- based ink that print on the coated screen directly, it will be a big saving if printing color is complicated.
2. Higher precision. the nearest drop on demand piezo print head can print each dot to the screen with high resolution. Machine build under industrial level, dual ball screw go with linear rail for the Y axis motion, drived by the AC servo motor, PLC controller. can match the mechanical precision with 0.015mm. The X axis print head motion system use the original Mimaki JV33 printing system, it use the THK linear rail go with encode film for decode position.
3. Higher resolution. Cts-180ES can get the screen printing resolution from 360dpi to 2880dpi, 360dpi / 540dpi / 720dpi / 1080dpi / 1440dpi chose optional.
4. High screen quality. Since there is no film, exposure time decreases and the amounts of light scatter and stencil undercutting are greatly reduced. Film dust and scratches also aren't a headache for the screen maker.
5. Fast speed, printer have 8 printing channel, can get high speed by 5min./square meter.
6. Super printing size. can print on any screen size small than 1800mm * 2500mm, bigger size can be also made custom.
7. Screen repeatability. each printed screen can be used again after using flushing.
8. Effective. Without film exposure, film sticking. super size can print on big screen, also save the time for splicing.
9. Multi functional. Change the water based ink screen ink to digital textile ink, it can use as a digital textile printer, such as print on T-shirt, bag, silk, pillow, pain wall paper etg. any soft textile. Change the ink to eco solvent ink, it can use as a digital flatbed printer, can print on the ceramic tile, glass, wood, pen, USB, metal etg. any rigid objects.
4. Specification:
Model
|
CTS-180ES
|
Max.Screen size
|
1800mm*2500mm (Can be custom made)
|
Resolution
|
360dpi / 540dpi / 720dpi / 1080dpi / 1440dpi
|
Engraving speed
|
average 4~8Min./m²
|
Model of print head
|
Piezoelectricity drop on demand DX5
|
Nozzles of inkjet head
|
180*8
|
Nozzle channel
|
8 channel
|
Head adjustment
|
Automatic / Manual
|
Engraving ink
|
Water based / Solid wax
|
Ink supply system
|
Negotive vacuum continus ink supply system
|
Acceptable file format
|
BMP/TIFF
|
Interface
|
100Base-tor, 100Base-tx, USB2.0/LPT
|
Operation system
|
MacOS, Windows 98 / Me / 2000 / XP / XP x64 / Vista*4 / Win7
|
X axis motion
|
AC servo motor, THK linear rail
|
Y axis motion
|
AC servo motor, dual ball screw
|
Control system
|
Industrial PLC electric controller
|
Operation interface
|
Touch screen
|
Temperature
|
20~30¡æ
|
Humidity
|
55~80%
|
Authentication
|
CE, ISO9001
|
Power
|
220V 50HZ/ 110V 50HZ, 1.8KW
|
Machine size
|
2500mm * 2400mm * 1000mm
|
Packing size
|
2650mm * 2550mm * 1100mm
|
Gross w. / Net w.
|
680KG/600KG
|
5. Main features:
1. Super engraving printing size, printing on any screen size freely. 1800mm engraving width and 2500mm, 3500mm or bigger
length can be made custom.
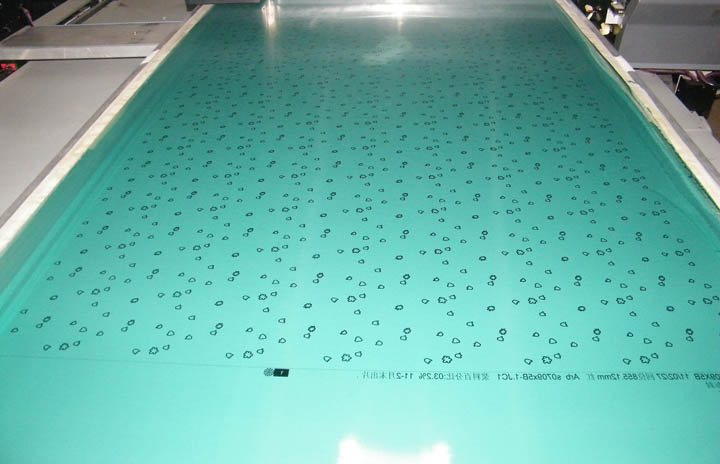
2. Industrial PLC electric control system.
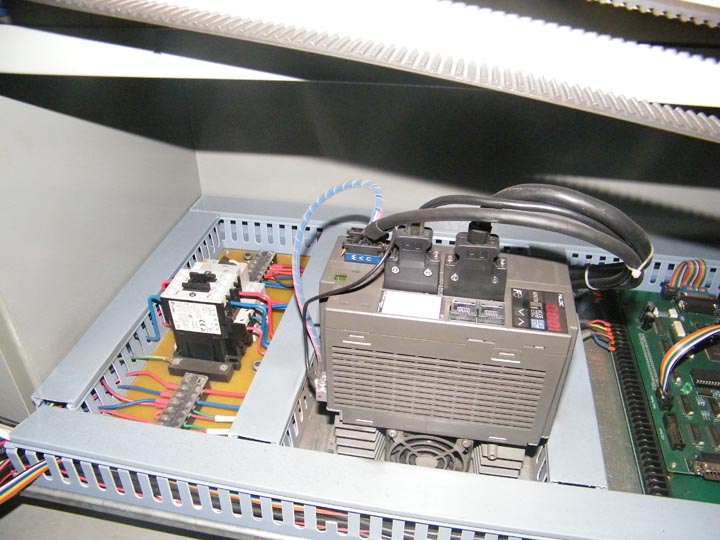
3. AC servo motor drive the flatbe motion with high precision.
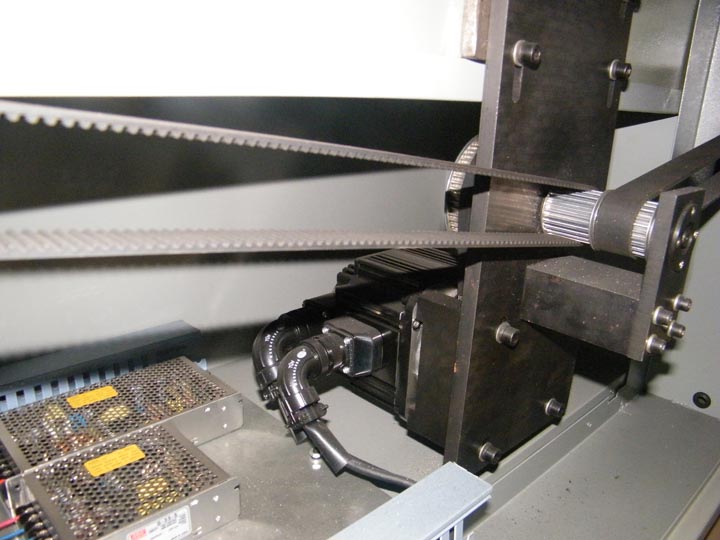
4. Dual linear rail and dual ball screw mounted at each side make the printing moving smoothly.
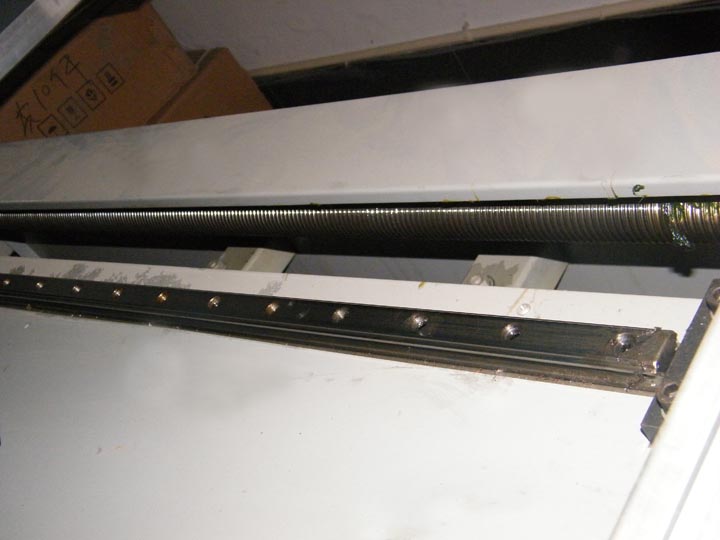
5. Humanistic design of head scratch protection height sensor can measure the gap between screen and head automatically.
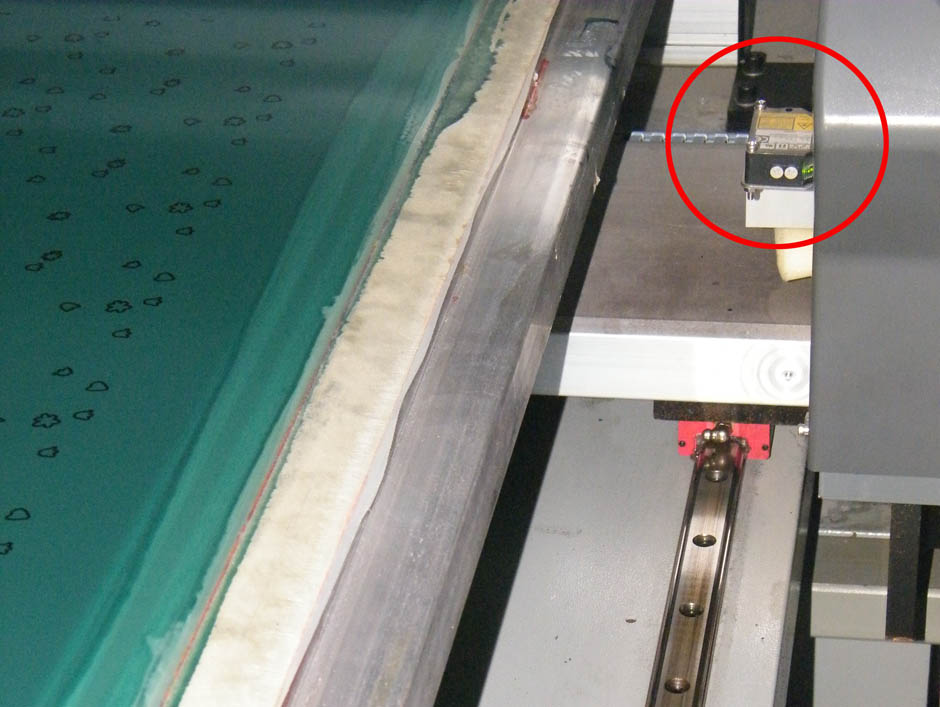
6. Can choose each team of nozzles printing freely by 12 ink channel.
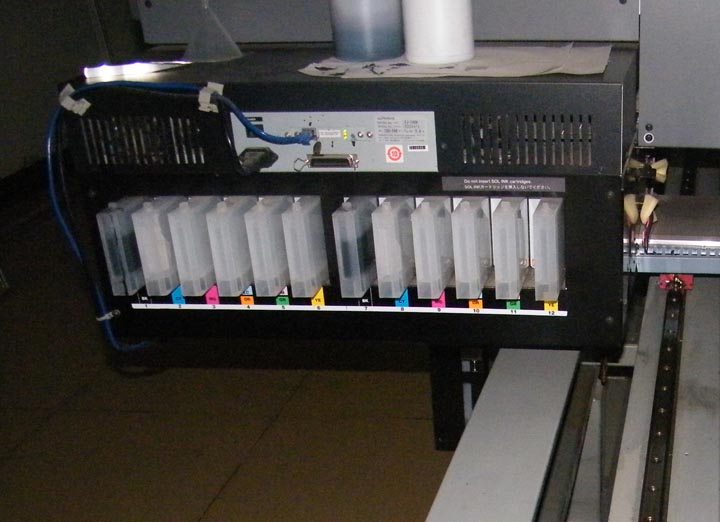
6. The workflow of Focus CTS-180ES flat bed engraver machine.
1. Color separation. separate each color from Photoshop. coreldraw or other professional color separation software.
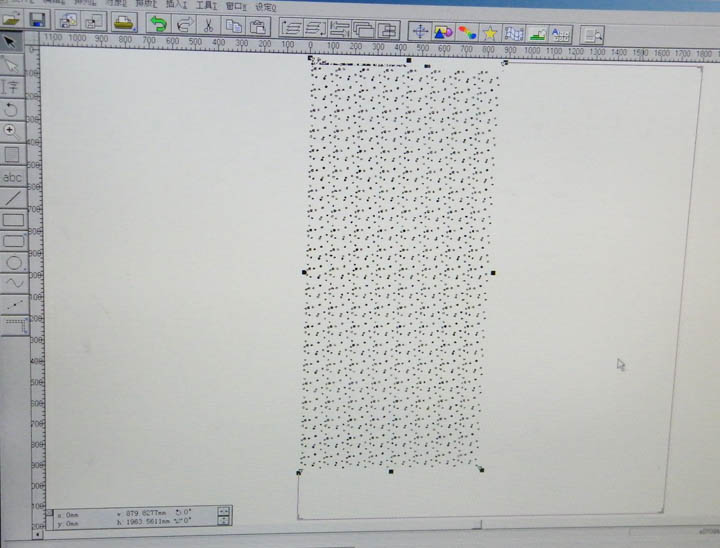
2. Screen loading. Coated screen preparing. Make the screen size with needed. coat with emulsion, then Load the screen to the printer flatbed. tighten
the screw at each angle of flatbed horizontal.
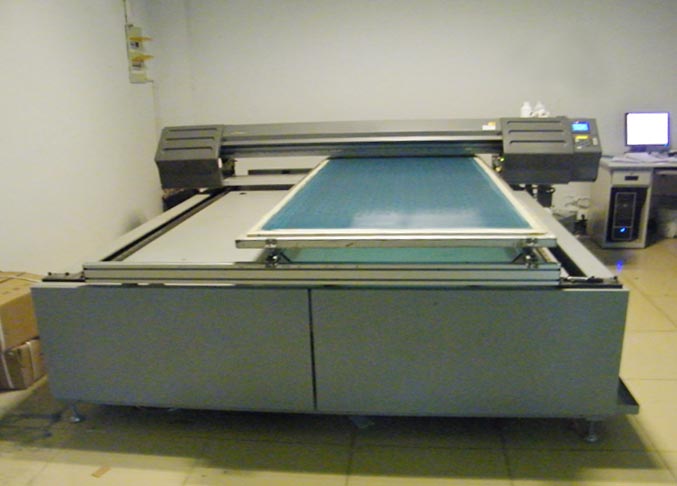
3. Printing. Start printing from computer directly.
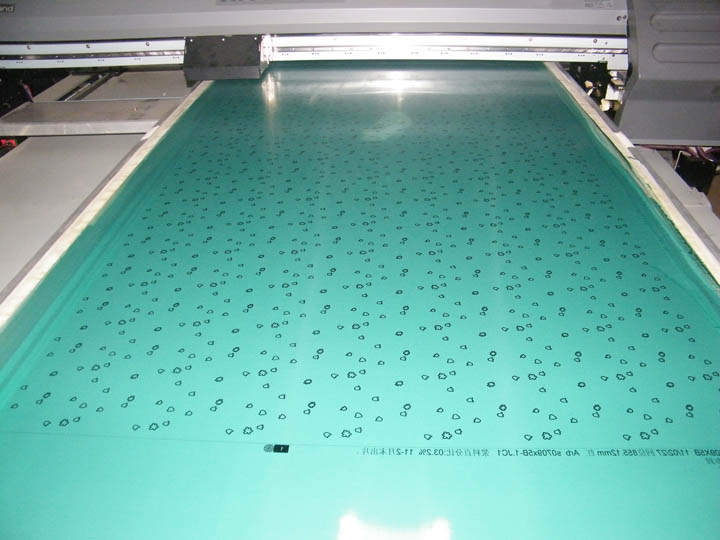
4. Developing. develop the printed screen under the light.
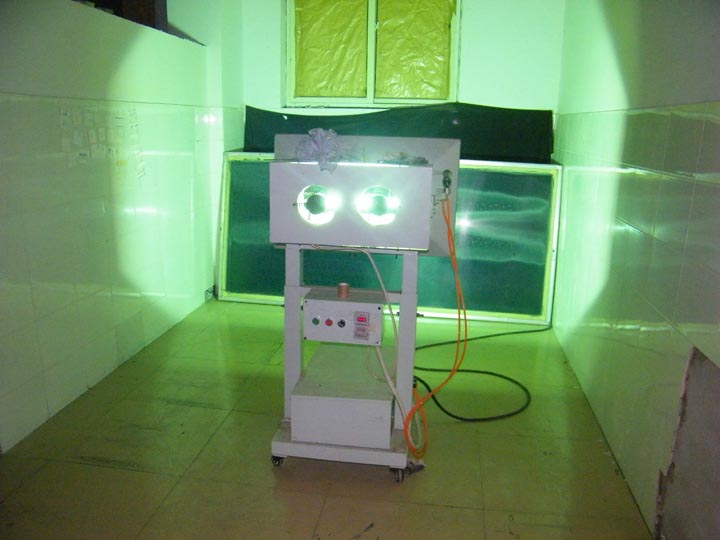
5. Washing, the print jetted ink will be washed off because it is wate based ink.
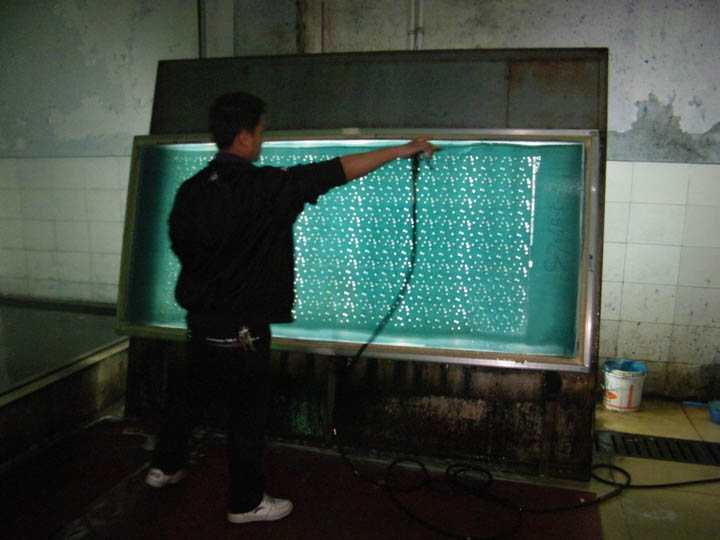
6. Heating.
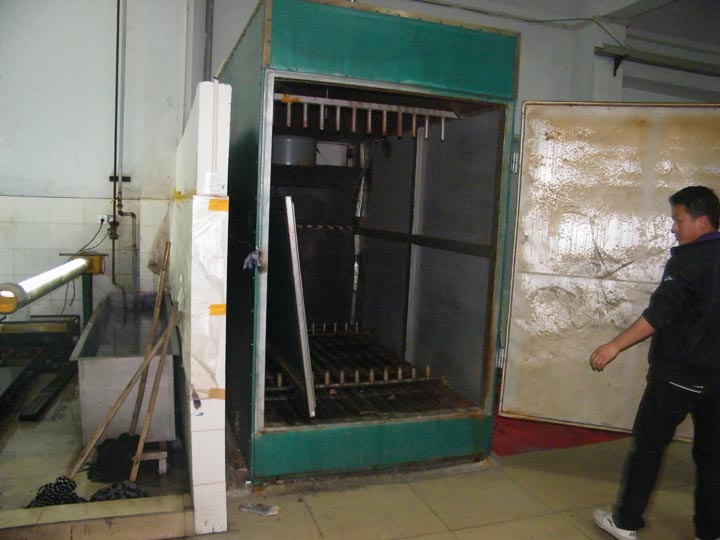
Finish. After the above 6 steps, the finished screen can be used for screen printing now.
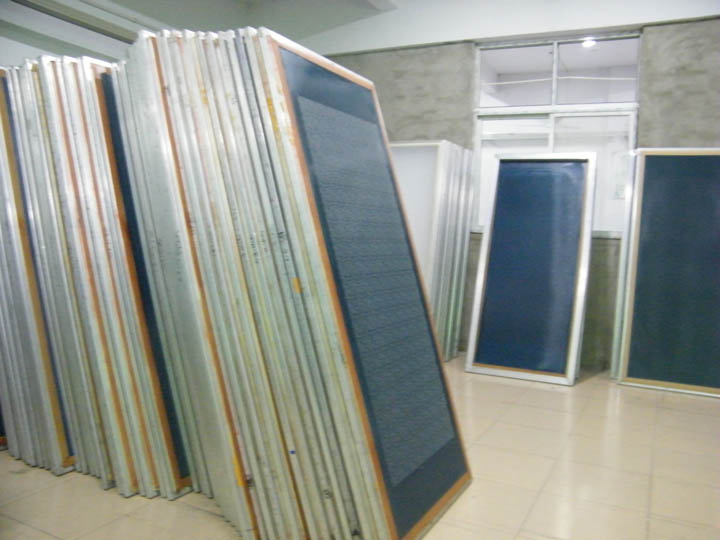
------Authored by Focus digital techmology co.,ltd. support team.
|